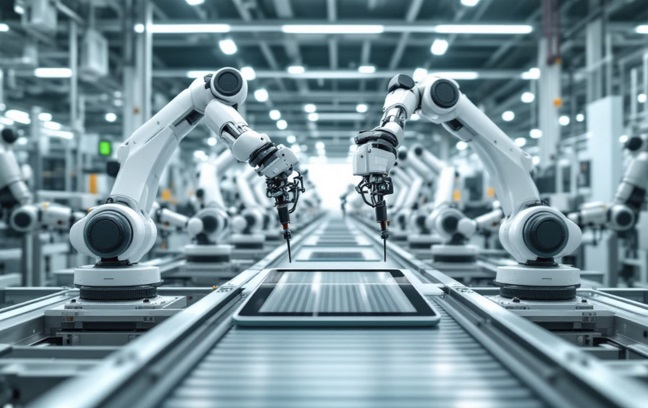
5 Errores Comunes en Proyectos de Automatización Industrial
La automatización industrial es la columna vertebral de la eficiencia y la competitividad en la manufactura moderna. Sin embargo, no todos los proyectos de automatización son un éxito rotundo. De hecho, la complejidad inherente a la integración de nuevas tecnologías puede dar pie a errores costosos que afectan plazos, presupuestos y, en última instancia, la productividad.
Para ingenieros, gerentes de planta y técnicos, identificar y evitar estas trampas es fundamental. Aquí analizamos 5 errores comunes y ofrecemos consejos prácticos para superarlos.
1. Definición Inadecuada del Alcance y Objetivos
Uno de los errores más frecuentes es lanzarse a un proyecto sin una comprensión clara y detallada de lo que se quiere lograr. Un alcance mal definido puede llevar a constantes modificaciones, sobrecostos y un producto final que no satisface las necesidades reales.
- El Error: No establecer objetivos SMART (Específicos, Medibles, Alcanzables, Relevantes, con Plazo Definido). No involucrar a todos los stakeholders clave (producción, mantenimiento, calidad, IT) desde el inicio.
- Cómo Evitarlo:
- Involucra a todos: Realiza reuniones multidisciplinarias desde el principio para entender las necesidades de cada departamento y asegurar que todos los requisitos operacionales, de seguridad y de mantenimiento sean considerados.
- Documenta exhaustivamente: Crea un documento de especificaciones de requisitos (URS) claro y conciso. Define qué se automatizará, cómo, qué se espera lograr (ej. reducir el tiempo de ciclo en un 15%, disminuir rechazos en un 5%), y cuáles son los límites del proyecto.
- Prioriza: No intentes automatizarlo todo de golpe. Identifica los "puntos débiles" más críticos y enfócate en ellos primero, expandiendo el proyecto en fases si es necesario.
2. Subestimación de la Complejidad de la Integración
La automatización rara vez se trata de instalar un solo componente. Implica la interconexión de sistemas legacy con nuevas tecnologías, diferentes protocolos de comunicación, software y hardware de distintos proveedores. Ignorar esta complejidad es una receta para el desastre.
- El Error: Asumir que los sistemas "hablarán" entre sí sin problemas. No realizar pruebas de compatibilidad y comunicación antes de la implementación a gran escala. No considerar la ciberseguridad industrial.
- Cómo Evitarlo:
- Mapeo de la arquitectura: Realiza un diagrama detallado de cómo se conectarán todos los equipos y sistemas (PLCs, HMIs, SCADA, MES, ERP, sensores, actuadores). Identifica los protocolos de comunicación y las posibles brechas.
- Pruebas de concepto (PoC): Antes de la inversión masiva, implementa pequeñas pruebas para verificar la compatibilidad de los equipos y la viabilidad de la comunicación.
- Considera la ciberseguridad: Desde el diseño, piensa en cómo proteger la red industrial. La integración abre puertas, pero también potenciales vulnerabilidades.
3. Falta de Capacitación y Resistencia al Cambio
La tecnología más avanzada es inútil si el personal no sabe cómo operarla o si se resiste a adoptarla. Un error común es enfocarse únicamente en la implementación técnica y descuidar el factor humano.
- El Error: No invertir en programas de capacitación adecuados para operadores, técnicos de mantenimiento y supervisores. No comunicar los beneficios de la automatización al personal.
- Cómo Evitarlo:
- Formación estructurada: Desarrolla planes de capacitación que incluyan formación teórica y práctica intensiva. No solo cómo operar, sino cómo solucionar problemas básicos.
- Involucra al personal: Desde las etapas iniciales del proyecto, involucra a los futuros usuarios. Pide su opinión y hazlos parte de la solución. Esto reduce la resistencia al cambio.
- Comunicación constante: Explica claramente por qué se está automatizando, qué beneficios traerá para la empresa y para ellos (ej. menos tareas repetitivas, mayor seguridad, nuevas habilidades).
4. No Prever el Mantenimiento y la Escalabilidad Futura
Un proyecto de automatización exitoso no termina con la puesta en marcha. La falta de una estrategia de mantenimiento y la incapacidad de escalar el sistema con el tiempo pueden convertir la ventaja inicial en un dolor de cabeza.
- El Error: Pensar solo en la instalación inicial. No definir planes de mantenimiento preventivo y predictivo. Seleccionar tecnologías propietarias que limiten la futura expansión.
- Cómo Evitarlo:
- Diseño para la mantenibilidad: Elige componentes estandarizados y fáciles de reemplazar. Documenta el código de programación de forma clara y con comentarios.
- Plan de mantenimiento: Desarrolla cronogramas de mantenimiento preventivo para los nuevos equipos y sistemas. Considera implementar herramientas de mantenimiento predictivo para anticipar fallas.
- Visión a largo plazo: Opta por arquitecturas abiertas y escalables. Considera la posibilidad de añadir más líneas de producción o funcionalidades en el futuro. ¿El sistema elegido puede crecer contigo?
5. Ignorar la Gestión de Riesgos y los Planes de Contingencia
Todo proyecto de automatización conlleva riesgos, desde fallas técnicas hasta problemas de seguridad o interrupciones imprevistas. No tener un plan para mitigar estos riesgos es una irresponsabilidad.
- El Error: Subestimar los riesgos potenciales. No tener planes de respaldo (backups) para el software y la configuración. Carecer de un protocolo claro para responder a fallas del sistema.
- Cómo Evitarlo:
- Análisis de riesgos proactivo: Identifica los posibles puntos de falla en el hardware, software, red y energía. Evalúa su probabilidad y su impacto.
- Planes de contingencia: Desarrolla procedimientos detallados para cada escenario de riesgo. ¿Qué hacer si falla un PLC? ¿Qué pasa si se pierde la comunicación?
- Backups y recuperación: Implementa un sistema robusto de respaldo para el código, la configuración y los datos. Asegura que los planes de recuperación ante desastres sean conocidos y probados.
- Pruebas de seguridad: Realiza pruebas de seguridad (ej. simulación de ciberataques) para identificar y corregir vulnerabilidades.
Conclusión
Los proyectos de automatización industrial son inversiones significativas que pueden transformar una operación. Evitar estos errores comunes no solo optimiza el proceso de implementación, sino que garantiza que la solución final sea robusta, escalable y, sobre todo, aporte el valor esperado, impulsando la productividad y la competitividad de la empresa. La planificación rigurosa, la comunicación constante y una visión a largo plazo son tus mejores aliados.
Contactanos hoy y empezá a transformar tu proceso industrial.